report on SUSTAINABILITY
Clover’s business is conducted taking into account our legal, ethical and economic responsibilities.
Introduction
This Report on Sustainability incorporates both the requirements of the Companies Act, 71 of 2008 (the Act) in terms of Regulation 43, as well as the King Report on Governance for South Africa 2009 (King III) regarding responsible corporate citizenship. The report also deals with the most relevant and material issues that could substantially impact on Clover’s ability to create and sustain value for its stakeholders going forward. Clover is one of few South African businesses that have been in existence for well over 100 years, and we recognise that in order to survive and prosper, we need to be concerned with sustainability.
The Social and Ethics Committee has considered the sustainability issues that are pertinent to Clover. The responsibilities and functioning of the Social and Ethics Committee (“Committee”) is governed by formal terms of reference approved by the Board and is subject to regular review. The main objective of the Committee is to assist the Board in ensuring that Clover remains a responsible corporate citizen with sustainable business practices by monitoring, developing, reviewing and enhancing the Group’s social, ethical, environmental impact and governance in terms of Regulation 43 of the Act, and King III.
To accomplish these above-mentioned tasks, the Social and Ethics Committee has developed and adopted a formal work plan entailing the functions as set out in Regulation 43 of the Act and King III. The implementation of this work plan is prioritised to enable the full discharge of its statutory functions over a period of three years. The Board supports the Committee by setting the appropriate tone and its behaviour, and communications contribute to Clover’s ethical culture. This report describes the work and conclusions of the Committee in its second year of establishment.
Over and above the requirements of the Act, the scope of the report has also taken into consideration the Sustainability Reporting Guidelines of the Global Reporting Initiative. In short, it attempts to summarise the key aspects of Clover’s business that are critical to its long-term future.
Governance and compliance considerations
Scope
The scope of this review covers Clover’s South African operations and will over time be extended to its subsidiaries in other countries.
Although King III requires that sustainability reporting be independently assured, the Committee is of the opinion that it would be premature to obtain external assurance until the Group’s social and environmental recording systems are mature. Clover has processes to ensure compliance with all applicable legislation and legal requirements. It is the Group’s intention to enhance qualitative and quantitative information as systems are progressively bedded down. Major improvements in this regard were made during the year under review, specifically with regard to Clover’s employment equity plan, employee training and development, the formalisation of the Group’s Social and Ethics policy as well as its policy on environmental impact.
In addition, Clover monitors and takes cognisance of relevant legislation, other legal requirements and prevailing codes of best practice, with regard to social and economic development, good corporate citizenship, the environment, health and public safety, consumer relationships, as well as labour and employment. All material risks in complying with the above sustainability drivers are incorporated into Clover’s risk universe and are monitored under Clover’s risk management process as described more comprehensively under the Governance section of this report.
Furthermore, legal compliance with Regulation 43 of the Act is described fully under the Sustainability section of this report, while compliance with Clover’s regulatory universe is described under Compliance in the Governance section. All legal compliance falls under the supervision of the Company Secretary who ensures that the full regulatory universe is monitored.
It is the Group’s intention to further incorporate prevailing codes of best practice in terms of Regulation 43 in future. During the year under review, the Social and Ethics Committee has monitored and assessed Clover’s standing under the headings set out below. In the opinion of the Committee, based on the information provided to it, the statements set out below fairly reflect the standing of the Clover Group.
Ethical leadership and good corporate citizenship
Ethical leadership
- Clover and its leaders have embedded a philosophy that
respects the rights and dignity of others. At Clover we are
aware of how our decisions influence others, and these
principles are integrated in our thinking and decisionmaking
processes. Our ethical leadership principles
are an integral part of our vision and mission, and are
demonstrated by our projects.
- Effective leadership based on an ethical
foundation
Clover’s strategy to build a sustainable business considers the long and short-term impacts of our operations on the economy, society and the environment. It is our intention not to compromise the natural environment, and we consider the impact of our operations on internal and external stakeholders. - Promotion of equality, prevention of unfair
discrimination and reduction of corruption
Clover is committed to the promotion of equality, and prevention of unfair discrimination with all its stakeholders, as is demonstrated in the Clover Ethics policy. We are committed to using our best endeavours to adhere to the following principles:- The United Nations Global Compact principles.
- The Organisation for Economic Co-operation and Development (OECD) principles on corruption.
- International Labour Office (ILO).
In order to ensure compliance to these principles, Clover’s Human Resources function and Risk Department conduct annual evaluations of the Group’s performance. Based on the evaluations performed for the year under review, no material deviations were reported.
Our Ethical Leadership principles dealing with corruption are further disclosed in our Report on Governance, Risk and Compliance. Ongoing awareness is raised through Clover’s Ethics awareness sessions at all operations for purposes of enforcing Clover’s ethical principles as described in Clover’s Ethics policy on Clover’s website.
- Effective leadership based on an ethical
foundation
- Good corporate citizenship
Clover’s business is conducted taking into account our legal, ethical and economic responsibilities. We aim to create higher standards of living and quality of life in the communities in which we operate, while still preserving profitability for our shareholders.- Corporate social and community investment
The purpose of the Clover Mama Afrika project is to identify women who are already making a difference in their communities and help them to become self-sustaining women with skills they can utilise to derive income in order to support orphaned and abused children, the elderly and infirm.
Once having learned these essential skills, our Mamas then pass on their knowledge and teach others in their communities to empower themselves and uplift their communities.
Well into its ninth year, Clover Mama Afrika Trust currently has 36 Mamas countrywide who collectively care for over 14 200 children and more than 2 500 elderly.
Clover Mama Afrika is based on a simple but powerful concept of empowering community caregivers with viable skills, which they in turn pass on to others, in order to earn a sustainable income for the community. This is done whilst caring for society’s most vulnerable members, including orphaned and abused children, HIV/Aids victims and neglected senior citizens. - Value drivers
Skills selection centres: Relevant, employable and marketable skills are aligned to the needs of each respective community to ensure that the centres become self-sustainable. After skills-training, Clover Mama Afrika provides start-up equipment to allow for immediate income generation and passing on of skills.
Site improvement: Clover Mama Afrika assists communities with the repairs and renovations to basic facilities such as appropriate ablution facilities.
Monitoring and evaluation: Regular monitoring and evaluation of each self-help project is implemented, which allows for the identification of strengths and weaknesses on an individual basis. Immediate support and assistance is provided where necessary.
Partners: Blue chip partners contribute to the success of Clover Mama Afrika and co-fund 43% of the Trust’s expenses. Blue chip partners include:- Expeditors International.
- HCI Foundation.
- Eqstra Flexi Fleet.
- MiX Telematics.
- Plascon.
Skills training Clover Mamas/
members trainedOperating
centresSkills transferred to
community membersGainfully
employed
membersSewing 101 29 640 93 Bread oven project 503 27 1 049 114 Cooking and baking 79 27 519 69 Food gardens 549 25 577 36 Quilting 39 15 165 12 Crochet/beadwork 49 35 553 37 Hairdressing 16 3 16 12 Pottery 1 1 20 2 Added value skills training Art 40 31 263 21 Flower arrangement 37 11 244 18 Mobile phones 79 30 10 MKI Health Information 18 18 Reach 20 000+ n/a Save a child 175 13 Basic admin/finance 27 27
- Awards Clover Mama Afrika has won prestigious awards since the inception of the project:
2005 – PMR Diamond Arrow Award
2005 – PRISA Prism Gold Award
2005 – Proudly SA Homegrown – Bridge Builder of the Year Award
2006 – Proudly SA Homegrown – Corporate Social Investment of the Year Award
2008 – PMR Gold Arrow Award
2009 – PMR overall Diamond Arrow Award
2010 – FoodBev SETA Baobab Award
2010 – PMR overall Diamond Arrow Award
2010 – Mail & Guardian Investing in the Future Award – Corporate category
2011 – Proudly SA Homegrown – CSI Champion of the Year Award
2012 – PMR Diamond Arrow Award
Clover Mama Afrika has positioned itself as a successful, award-winning example of a sustainable and effective CSI project, which is making a real difference in the lives of many needy South Africans.
Based on the most recent B-BBEE verification performed by EmpowerLogic, Clover achieved a full allocation of available points under the Socio-Economic Development section of the B-BBEE balanced scorecard.
- Corporate social and community investment
- Record of sponsorship and charitable givings
Clover’s sponsorship budget for the period under review was submitted and approved by Executive management. Management is responsible for the tracking, accounting and reporting to the Social and Ethics Committee all sponsorships, donations and charitable givings. Supporting documentation is maintained by each business unit to enable transparent reporting.
Sponsorships are used with a purpose of gaining brand awareness, corporate identity or consumer loyalty, which is aligned with Clover’s vision and mission.
Social and economic development
Clover’s business aims to enhance GDP, life expectancy, literacy and levels of employment. As required by regulation 43(5)(a)(i)
of the Companies Act (Act 71 of 2008), and to the extent that it is incorporated into South African legislation, the Social and Ethics Committee monitors Clover’s activities around Social and Economic Development with regard to matters relating to:
- The 10 United Nations Global Compact (UNGC) principles
The universal principles to which Clover is committed to include human rights, labour, the environment and anti-corruption, as listed below:
- The OECD recommendations on corruption
Clover is committed to conducting its business activities lawfully and in a manner that will enhance the qualities valued by Clover, in particular, ethics, integrity and compliance with the law. Corruption can occur in many forms including extortion, nepotism, embezzlement, bribery, cronyism, patronage amongst others. Corruption impacts directly or indirectly on sustainable development of Clover’s stakeholders.
Clover’s business processes, employee behaviour and daily activities at all levels of the organisation are conducted in accordance with the OECD recommendations on corruption. Further disclosure on the compatibility of corruption can be found in our reports on Risk Governance and Compliance.
- The Employment Equity Act
Clover subscribes to Employment Equity legislation and relevant Codes of Good Practice; this is also encompassed in the Clover Employment Equity Plan. There should be no unfair discrimination in respect of inter alia, race, colour, language, religion, gender or political views or on the grounds of disability. Therefore all employees will receive equal opportunities to develop according to their merit and ability.
In line with the requirements of the Employment Equity Act, Clover has drafted its Employment Equity plan. The objectives of the plan are to give effect to the company’s employment equity policy in so far as it relates to employment equity goals. The employment equity plan will also ensure that Clover’s workplace remains free of unfair discrimination and reasonable progress is made towards employment equity in the workplace. The Executive Committee is responsible for the implementation and monitoring of Clover’s employment equity plan. The Social and Ethics Committee, in execution of its duties, will assign specific responsibilities to individuals and managers in general. The responsibility to implement employment equity plans at the different Clover workplaces is delegated to site managers. All appointments should be conducted in line with Clover’s employment equity policy. Clover’s HR is responsible to monitor these activities and report to the Social and Ethics Committee at least annually on progress to monitor EE targets.
- PERCENTAGE OF STAFFPercentage of staff from designated groups
Clover defines designated groups in line with the Employment Equity Act. A designated group means black people, women, or people with disabilities. Clover has been increasing the number of employees from designated groups as tabled on the right: - Employment Equity Plan objectives
To improve diversity in the workplace, and especially to address the levels of representation of people from designated groups, Clover is committed to achieving the goals set out below:
Employment Equity measurements against objectives Target
30 June 2013
%Achieved
30 June 2013
%Objective
30 June 2014
%Improve representation as follows: Black people on F Band 14,20 14,29 14,20 Black people on E Band 5,00 9,52 9,50 Black women on E Band 0,00 4,76 4,70 Black people on C5 – D5 Band 17,90 19,32 20,00 Black women on C5 – D5 Band 4,80 5,40 6,70 Black people on C1 – C4 Band 51,00 53,50 52,40 Black women on C1 – C4 Band 9,90 10,67 10,60 Disabled people 0,77 0,72 0,85
- Training and development
Training objectives 2013 2012 2011 2010 2009 Average number of employees 6 533 6 555 6 353 6 362 6 579 Employee turnover per year (%) 10,0 8,21 10,9 9,3 10,3 Number of man days lost due to strikes 11 118 346 112 334 415 Total training spend per year (R’000) 7 965 4 879 3 450 3 942 7 017 Number of employees trained 1 953 2 224 2058 1 550 3 133 Training spend per total number of employees per year (R) 1 219 744 543 619 1 066 Number of man days spent on training 4 627 2 965 2 744 2 067 4 177
Clover has embarked upon various training initiatives to uplift previous disadvantaged individuals. The diagram below summarises the salient features of our training programmes:
Total employees Black Employees Number of employees trained 1 953 1 601 Number of bursaries granted to employees/students
to complete Degree and Diploma Studies54 23 Value of bursaries granted for Degree and Diploma Studies R720 000 R453 000 Number of trainees on Workplace Experience and
In-Service Training Programmes24 17 Number of employees enrolled on Learnerships and Skills Programmes and Apprenticeships 299 266
- The Broad-Based Black Economic Empowerment Act.
Clover sees Broad-Based Black Economic Empowerment (B-BBEE) as an opportunity to increase economic activity thereby creating sustainable livelihoods for the country’s inhabitants, as well as a growing sustainable consumer market.
Clover is currently a Level 6 B-BBEE contributor. The Group subscribes to the National Government’s priorities with regards to transformation and empowerment and embraces the principles of B-BBEE. It seeks to remain a positive and constructive contributor to the country.
For this reason, the Group is aligning its overall business strategy with a B-BBEE strategy to achieve a higher level of compliance.
During the year under review, Clover appointed EmpowerLogic to benchmark its current levels of B-BBEE compliance against the newly issued Agri-BEE sector codes which were published in December 2012. The results of this assessment form the basis of Clover’s June 2013 scorecard and have been used to identify key actions, and to determine the necessary focus areas to achieve a higher level of compliance.
Clover currently scores relatively well in areas of preferential procurement, enterprise development and socio-economic development. In terms of its strategy, the Group will pay particular attention to areas of equity ownership, management control, employment equity and further skills development.
Environment, health and public safety
Clover strives to manage its business in such a manner that the environment is adequately protected, and the use of natural resources is minimised and that environmental management programmes are established to contribute towards the sustainability objectives of the company.
Clover’s green initiative strategy was formalised and commenced in the 2011 financial year with the aim of establishing a formal environmental sustainability (“green”) strategy. In terms of achieving this vision, Clover recognises its responsibility to reduce, and as far as possible, to eliminate the impact of its business on the environment. Clover recognises that in achieving environmental excellence, it would obtain a competitive advantage over its peers, as a food manufacturer’s energy and services costs comprise approximately 30% of fixed costs.
This responsibility not only relates to operations within Clover’s control, but also to Clover’s supply chain partners, who in the course of supplying Clover, could be responsible for significant environmental impacts.
In the realisation of this responsibility, Clover has developed an environmental management system (“EMS”) which provides a structured framework against which continuous improvement can be measured.
Clover actively monitors environmental, health, safety and quality through the use of its dedicated Entropy risk management system and other forms of assurance. It is envisaged that the Entropy measurement will be progressively extended to other areas of environmental sustainability.
Table of different types of monitoring performed by the Group
Objective | Outcome | ||
Continuously improve on environmental performance. | Implement and maintain an effective environmental management system (“EMS”). Provide a structured framework for continual improvement. | ||
Inform staff on the EMS and policy and equip them with skills to achieve requirements of the policy. | Staff engagement, formal development and training. | ||
---|---|---|---|
Ensure consistent quality of products in line with legal, regulatory and best practise requirements. |
|
||
Reduce carbon footprint. |
|
||
Reduce water usage across operations. |
|
||
Limit the generation of solid and liquid waste and the impact of their disposal. |
|
||
Minimise returns and damages and the impact thereof on the environment. | Implement programmes and monitor. | ||
Reduce energy consumption and associated emissions. | Monitor energy usage and set targets for reducing consumption. | ||
Manage impacts for on-site storage of fuels and chemicals, both during normal operation and in the event of spills and emergencies. | Implementation and monitoring of procedures. | ||
Optimise the use of primary and secondary packaging. | Monitor wastage and implement improvement processes and targets. | ||
Adhere to all applicable environmental legislation. | Continuously review and revise the ambit and effectiveness of the EMS. | ||
Ensure continuous monitoring of and reduction in the impacts associated with milk supply. |
|
||
Inform supply chain partners on activities to reduce environmental impact and partner with them to reduce their own impact. | Formally engage with partners in the supply chain. | ||
Ensure Health and Safety throughout all operations. | * Continuous monitoring to ensure safe working environment. |
Clover requires each business unit to regularly report its contribution to the environment on agreed measures to the Social and Ethics Committee.
The Chief Engineer: Maintenance and Safety, Health and Environment (“SHE”) for Production together with the Divisional Engineer for Distribution are both responsible for reporting on Clover’s green strategy and on SHE compliance to the Social and Ethics Committee on a quarterly basis.
- Quality
- Quality of raw milk collected
Clover’s Milk Procurement business unit continuously seeks new and better ways of conducting its business. It has finalised its Electronic Tanker Collection System (“ETCS”) during the financial reporting period. This is a first for the South African dairy industry and is a huge improvement over the methodologies used in the past. Although we had some difficulties to resolve during the test phase, we are confident that all these challenges will be addressed and that this system will add value to Clover and its milk producers in future. The main benefits of this new system are:- Automation of transfer of milk from the tanks to the Clover milk system.
- Human interference is limited to the absolute minimum during the milk collection process, to ensure the best possible levels of accuracy, repeatability, consistency and hygiene.
- Reconciliation of milk volumes can be done within minutes after off-loading at factories, due to the availability of data.
- Quality over final product produced
All Clover products are produced in terms of International best practices, regarding quality, hygiene and food safety. All Clover factories are ISO 9001 and HACCP certified and accredited by third party auditors and comply with all international standards, required for food safety and quality management systems.
Clover Quality Assurance performs various tests in all stages of the production process of all its products, through highly trained technicians, in well-equipped laboratories to ensure constant quality, food safety and meeting minimum legal regulatory requirements.
Producer selection Clover sources milk from 231 carefully selected producers Ongoing quality assurance 55 quality checks on fresh milk that starts the second it is collected Clover way better approach to work Clover’s production systems are flushed every eight hours to ensure freshness Clover Way Better supply chain and warehousing capabilities Delivering to 13 012 points through 583 trucks to an average eight customers per day per truck
- Quality of raw milk collected
- Carbon footprint
Clover’s carbon footprint extends over the operations of the following five business units:
Business unit Description/key activity Head office Corporate administration, marketing, management Procurement Transportation of raw milk and materials from suppliers to Clover facilities Production Facilities for the processing, packaging and dispatching of products Primary distribution Transport of products from production facilities to primary and secondary distribution centres Secondary distribution Clover controls a large number of secondary distribution facilities across South Africa that handles own and principal clients’ products. Distribution is to retail customers through leased vehicles, under the control of Clover
Summary of carbon footprint by scope Scope breakdown per business unit Business unit contribution
Production is by far the biggest emitter of greenhouse gas
Secondary distribution is the second biggest emitter
Primary distribution (inclusive of contractors distributing on our
behalf), has a marginally bigger footprint than Milk ProcurementActivity-based (non-scope) summary of emissions Emission source per business unit
- Electricity is the biggest emission source for Clover
- Coal is the second biggest, with diesel being the third
-
Refrigeration emissions is relatively small
-
Mobile combustion Stationary combustion Fugitive (refrigerants) Electricity Purchased steam
Production site emissions Production emissions by factory
Powder factories have out of proportion emissions due to high coal consumptionSecondary distribution site emissions - Waste and operational efficiency
During the reporting period, progress was made with the Cielo Blu project, which resulted in the movement of some facilities and operations (Clayville UHT to Pinetown & Port Elizabeth). The investment in ESL and UP milk, in addition to Cielo Blu, resulted in uneconomical production at Clayville for an extended period of time during the current financial year only. These temporary factors make direct comparison with the previous financial years difficult. In the new year once Cielo Blu project is finalised, it is expected that water and electricity usage will reduce substantially with usage forecasts reductions estimated at 21% by end 2014/2015. This impacted environmental performance, as plants were not running at optimal volumes, being at lower than expected production volumes that increases utilisation of water and electricity resources. Utilisation of these resources increases as a result of higher number of production batches than normal. This necessitates more stoppages after each batch and increases the number of washes for sterility after each batch, which results in more resources being utilised. Excluding the impact at Clayville, appropriate progress was achieved against targeted measures.
Working towards zero-waste operations 2013 2012 2011 Total waste generated by operations Total waste recycled (kg) 2 180 797 1 188 047 829 377 Reducing the amount of water used to produce products Water consumed per kg or litre of product produced (l) 4,1 3,5 3,7 Reducing Clover’s energy consumption Electricity consumed per kg/l product produced (kWh/kg) 0,171 0,1471 0,1567 Fuel consumed for steam generation (coal, gas, HFO) per kg product produced (kWheq/l) 0,41 0,4067 0,3921 Improving occupational health and safety performance (lost time injury (man days)) Incidents and injury reports throughout the Group’s operations 347 574 579
-
Electricity saving strategy
The current strategy revolves around the following components, with a targeted 20% reduction in actual resource use intensity by end 2014/2015 financial year. The capital expenditure budget was aligned to fund these objectives, and total expenditure to reduce utility consumption, increase efficiency, etc. amounts to R15 million for the 2013/2014 financial year.
Activity Implementation status Completion date Eskom subsidised lighting retrofit 5% 03/14 Condenser/cooling tower automation 0% 05/14 Steam Generation Automation 85% 03/14 CIP optimisation – reduced cleaning times 50% 02/14 Operator responsibility for energy consumption – daily monitoring and feedback 30% 10/13 Ensuring all plant components are synchronised without knock-on
delays – daily management feedback30% 10/13 Warm/cold piping insulation 85% 05/14 Ablution heat pumps 0% 03/14 VSD on all large motors above 15kW 75% 03/14 Power factor correction >0.98 90% 12/13 Increasing OPP >75% 70% 05/14 Fitment of new synchronous/VSD air compressors 60% 05/14
- Product responsibility over raw milk intake
Clover’s commitment to quality starts on the farms of its producers. In terms of Clover’s Best Farming Practices (“BFP”) programme, based on the International Dairy Federation’s directive, the following aspects are focused on:- Animal health and herd management
- Animal feed and water
- Animal medication and agricultural chemicals
- Milk hygiene and safety
- Environmental management
- Personnel and people
- Treatment and hygiene registers
- Required registers and records
Clover has integrated the above mentioned BFP programme into a much broader Clover Sustainable Dairy Model (“CSDM”) and the details of this programme were captured into a user friendly Microsoft Excel model, with the assistance of Volition. This model is now ready for implementation and given the complex and evolving nature of the programme, Clover intends phasing in the implementation over a number of years.
The preliminary focus areas are:- Herd management, including managing of greenhouse gas (“GHG”) emissions.
- Animal feed, pasture and soil management, including GHG emissions and retention.
- Water management and treatment.
- Animal medication and agricultural chemicals.
- Dairy parlour and equipment (including infrastructure, hygiene and safety).
- Milk composition and quality.
- Environmental management, manure handling and bio-diversity, including GHG emissions and reduction thereof
- Energy management and utilisation of alternative energy resources for the reduction of GHG emissions
- Bio-security, with the main focus on disease control
- Personnel and people
- Occupational Health and Safety
Employees can only operate efficiently and effectively in a safe and healthy working environment. Formal health and safety policies are in place as well as systems and processes to implement and monitor these. There is a standard health and safety procedure for every potentially dangerous substance or operation in the workplace.
All of Clover’s production facilities and major distribution facilities were audited by an accredited external party for safety during the review period. Measures complying with ISO14000 (Environmental Management) and the Occupational Health and Safety Act (“OHS”) were used. Audits are conducted yearly to monitor continuous improvement.
The following results were achieved (as a percentage of compliance with OHS):
Site Safety % 2013 Safety % 2012 Difference Frankfort 87 85 Heilbron 88 86 Clayville 97 91 Lichtenburg 93 93 Queensburgh 93 94 Estcourt 94 89 Bethlehem 94 92 Parow 94 92 Port Elizabeth 90 89 Mayfair Not audited* 92
Governing stakeholder relationships/consumer relationships
Throughout the 2013 financial year the Group has actively engaged with all its key stakeholders. Management have identified all material stakeholders as well as their legitimate interests in and expectations of the Group on a continuous basis as stakeholders’ interests in the Group are dynamic and subject to change. Once stakeholders are identified, management decides through consultation with the various stakeholder groups how to further engage with each constituency. This process forms part of the Group’s risk management framework.
As a result of Clover’s diverse business model, Clover interacts through a wide range of functions within the business with various stakeholder groupings on an ongoing basis. The Clover stakeholders that have been identified are all stakeholder groups that can materially influence the attainment of Clover’s strategic objectives, but also more specifically it is those groups, individuals or entities, who can be affected by the actions and operations of Clover or on the contrary who’s operations can materially impact on Clover’s operations.
Amongst all the major stakeholder groupings identified, Clover has a distinct criterion for its strategic stakeholder partners whose relationships are required for the Group to attain its future strategic objectives.
Clover's material stakeholders
Stakeholder engagement
Stakeholder Group | How we engage with our stakeholders | Their contribution to value creation | What our stakeholders expect from us | What concerns our stakeholders | Method of Governance |
Communities, traditional and civic society | Direct interaction through various corporate social investment initiatives and environmental campaigns in various communities | Participation with the community affords Clover the opportunity to understand their needs and to further align our business in a way that improves the lives of our communities at large | Ongoing commitment to our core strategic social investment initiatives adding to the wellbeing of the community |
|
Corporate Governance policies |
Consumers |
Promotions and community- based initiatives, social media, Clover consumer centre, Consumer Goods Council | Loyal consumers continued support of their most admired brands and trusted products | Providing high quality and trusted products of their most admired brands in fulfilling consumers’ needs |
|
Social media policy, Consumer crises policy, Competition Law policy, product quality assurance programmes |
---|---|---|---|---|---|
Customers/ Trade | Meetings, conferences and workshops, CSC taking orders from trade | Extensive retailer footprint providing the basis for continued growth. Clover’s brand expansion through retail expansion into Africa | Providing good quality products at competitive prices |
|
Service level agreements |
Employees/
Management |
Intranet, CE briefs, management and general staff briefings, Corporate bi-monthly newsletter(In Clover), workshops and conferences, training programmes, notice boards, intranet communication and performance reviews | Employees acting in accordance with Clover’s values of respect, integrity, fairness and responsibility form the foundation of our business. By providing Clover employees timely updated business information and relevant strategic information, Clover would embed its strategy while achieving company objectives | A stimulating and gratifying work environment, while offering prospects to meet career growth aspirations |
|
SHE Policy, EE Plan, Employment policy |
Government and regulating authorities | Personal meetings, written and verbal communication, through business organisations, Parliamentary portfolio committees | Government gives us our licence to operate and provides the enabling regulatory framework | Continued contribution to the economic growth and social upliftment of the communities in which we operate. Exercise good corporate governance practices while ensuring compliance with all applicable legislation |
|
Public participation |
Insurers |
Meetings and site surveys | Ensure Clover has insurance cover for material insurable loss events | Open and transparent communication enabling insurers to assess risk appropriately |
|
Insurance policies |
Media | Media statements and briefings, Social media pages | The media contributes in sustaining our brand reputation and increase awareness on new products, community development programmes and changes in our business strategy | Good Corporate Citizenship |
|
Protocol to respond to media set in social media policy |
Milk producers |
Circulars, regional individual and group meetings with producers, media and the Clover producer forums | Clover’s milk producers provide good quality raw milk used in manufacturing of our dairy products | A stable market for milk produced for delivery to Clover |
|
Producer agreements |
Principals | Contract and service level agreements, meetings, transactional information integrated via respective ERP systems | Participation in growing the footprint of retailers while achieving economies of scale and reducing costs in the supply chain | Timely delivery of ordered product with professional in store merchandising | Clover not meeting the agreed service levels in distribution and merchandising activities | Service Level agreements |
Shareholders, investors and analysts |
Investor presentations and road shows, circulars to shareholders, Integrated Annual Report, Annual General Meeting, Press releases, announcements and notifications through SENS, Clover website | Investors provide the financial capital necessary to sustain growth. Shareholders are encouraged to attend the company’s annual general meeting to vote on resolutions and to discuss relevant issues with the company’s directors and management | Providing sustained returns on investment by achieving business objectives through delivery on embedded strategy, sound risk management identifying strategic growth opportunities and good governance practices |
|
Price sensitive information policy, Insider trading policy, ERM policy, Governance policy |
Suppliers and service providers | Supplier meetings, site visits, performance evaluation and audits, business association meetings | Our suppliers provide us with good quality raw materials and services that enable us to produce quality products for our consumers | Conducting business in a transparent manner that is mutually beneficial and sustainable |
|
Procurement policies |
Trade unions |
Regular meetings with Unions and collective bargaining forums | To engage organised labour in a positive manner on matters affecting their members as well as matters of mutual interest | Positive work relationships in dealing with matters sensibly during the negotiation process | Provision of competitive remuneration packages and safe working conditions | Remco, collective bargaining agreements |
Consumer relationships, advertising, public relations and compliance to consumer protection laws
Regulation 43(5)(a)(iv) of the Companies Act (Act 71 of 2008) requires companies to monitor their activities around consumer relationships including the company’s advertising, public relations and compliance with consumer protection laws.
Consumer relationships
The Group’s strong and honest relationships with its consumers, principals, retail and wholesale businesses, agents and distributors, continued during the year under review. This ensures that the Group’s products reach consumers throughout South Africa in good condition and at market related prices in a very competitive market. Clover’s emphasis on quality products is strongly embedded in the quality raw milk which the Group procures from its producers.
Consumer relations are managed through the Clover Consumer Centre (“CCC”). The CCC strives to consistently service our consumers’ expectations and needs by demonstrating the required respect for their needs and opinions. All complaints and enquiries are handled professionally by trained consultants to ensure that the image of Clover, Clover’s brand names and services are protected, while ensuring compliance with the Consumer Protection Act. As required by the Consumer Protection Act, a procedure is in place and will be applied in situations where a serious risk or threat exists for Clover in general, Clover’s brand names or products, Clover’s personnel or on possible environmental impact.
Type of call | Description |
Priority 1 |
Critical calls
|
---|---|
Priority 2 | Client requests feedback in writing The complaint receives urgent attention and the consumer is kept informed by the head of the Consumer Centre until such time as the investigation is completed and complies with the requirements of the consumer. |
Priority 3 |
Client wants to speak with manager Complaints, which are not satisfactorily dealt with by the consultant and where the consumer insists on communicating with the head of the Consumer Centre, the complaint must be escalated to her for her attention. |
Priority 4 | Completed by consultants Complaints are attended to by the consultant with the information at hand and no further escalation of the complaint/incident is necessary. |
Consumer engagement and the Way Better philosophy
Clover’s corporate strategy is to build onto existing competencies within the Group and to establish a culture of exceptional performance with a view to creating a platform for future market expansion. Key to all of Clover’s activities is the expansion of capacities to share in the strong growth in consumption in the product segments in which it has a leading market share. Clover has identified a unique set of strategic pillars on which the success of the business is founded. The philosophy behind the Way Better initiative is therefore more than a marketing campaign. It represents a cultural step-change in seeking optimal ways of delivering on the corporate strategy and is aimed at setting new standards in best practice and to attract the best in the industry to Clover. The Way Better metaphor was created in order to engage and introduce Clover’s consumers to this enhanced approach to doing business. Although primarily a marketing campaign, Clover Way Better draws on Clover’s position as a market leader that innovatively adds value through convenience and quality as highlighted by the number of ideas and compliments that we received during the year.
Public Relations
Public Relations within Clover is managed through the Corporate Services department. No Clover employee may comment or conduct any interviews with the media on behalf of Clover. Media communication in Clover is restricted to two executive members namely Johann Vorster (Chief Executive), Jacques Botha (Chief Financial Officer) and Jacques van Heerden (Company Secretary). Written communications are outsourced to an external agency.
Compliance with Consumer Protection Laws
The Group has taken proactive steps to ensure that it is fully
prepared for the application of the Consumer Protection Act
(“CPA”). High-level induction programmes to key individuals
in the Group on the potential effect of the application of the
CPA are ongoing. The process of establishing a CPA Centre of
Excellence is in progress which will enable Clover to maintain
its commitment towards compliance with laws and regulations.
The marketing department provides the Social and Ethics Committee with a regular reports of its activities to enable the Social and Ethics Committee to monitor compliance to CPA. Furthermore logs are maintained for any promotional and trade coupon promotions in line with the CPA: Trade coupon and promotion policy, which are also reported to the Social and Ethics Committee.
The Company Secretary together with the Group Manager: Product Innovation and Technology are responsible for the annual review of the company’s compliance with regards to the following acts:
- Consumer Protection Act.
- Food stuff, cosmetics and disinfectants Act.
- Other labelling legislation.
Labour and employment
Project Driven
During the financial year, Clover launched Project Driven which
outlines the broad strategy for addressing the Human Capital’sresponse to:
Attraction and retention of employees
Clover recognises that there is a limited pool of skilled resources
available, and as part of our “Way Better” and “Driven” campaigns,
we aim to enhance the attraction and retention of employees.
Achieving our Vision and Mission is largely dependent on
Clover’s ability to attract and retain high-calibre individuals.
Change of the labour landscape
Clover recognises the need to assess and respond to the
dynamics in the social and labour environment on an ongoing
basis. Special focus is placed on optimising industrial relations
platforms at different levels in the Company. At Clover, we
respect the rights of our employees.
Productivity improvement
Productivity and continuous improvement initiatives are
part of the Clover culture. Through Project Driven there is
renewed focus on team performance, multiskilling, variable pay
opportunities and a number of other Way Better initiatives
Alignment of employees
We believe the alignment of employees is critical for business
success, and to build a culture of exceptional performance.
Our approach towards performance management and the
mechanisms that support individual and team performance
are being reviewed. A range of communication platforms are
used to enhance alignment – examples include management
breakaway sessions, team meetings, in-house publications,
union meetings, etc.
Skills
To secure Clover’s position as one of southern Africa’s leading fast moving consumer goods companies, the Group proactively engages in the development of employees in all disciplines.
Specific focus has been on Merchandiser Learnerships, technical training in our production facilities, the upskilling of sales personnel and management and leadership development. Financial assistance for study purposes was further extended, and a number of internships were introduced. Going forward, it is acknowledged that a range of new skill sets will be required. This will necessitate renewed focus on fast tracking, coaching and mentoring of young talent.
Strategic resourcing
The dynamic environment in which we operate and our expansion plans demand that we review our resourcing strategies. Project “Driven” will enhance how Clover attracts, engages, motivates and rewards our workforce, so as to maximise the likelihood of achieving our vision through developing and reinforcing a shared mindset.
Employment equity
The company fully supports employment equity in the workplace and various measures are in place to assist in reaching employment equity objectives. These include bursaries, internships and other employee development initiatives. (For further details refer to paragraph 4.3 above) as highlighted in the Employment Equity report.
Innovation and technology
We encourage innovation in Clover and acknowledge the need to equip personnel with technology that will enhance performance. A number of projects that will result in new generation business systems being introduced, are in progress.
Africa expansion
Our decision to exploit opportunities which exist in Africa are placing new demands on the business. The Human Resources function is assisting with the process of manning these operations.
Legislation
Clover is committed to conducting its business activities lawfully and ethically. To ensure compliance with legislation, measures are in place and regularly reinforced.
Clover’s strategy for continued sustainable development
- Economic viability
In order to remain economically viable, Clover needs to continuously evolve its business, partnerships and products. During the review period, Clover continued with its strategy of investing in and concentrating on branded and value-added products.
During the period under review, Clover commenced with the final phase of project Cielo Blu, the Group’s capital expansion and repositioning programme commissioned in 2011, with the move of the Mayfair beverages factory into the Clayville facility. The relocation of the Group’s dairy equipment to coastal regions has been completed and has drastically reduced supply chain management complications faced in the prior year. The savings from Project Cielo Blu’s capacity and efficiency improvements are delivering against expectation and are expected to fully accrue to Clover over the next year.
Cielo Blu has made a significant impact on the amount of fuel used for transporting product. Prior to the relocation of the production facilities closer to the milk source, Clover had to transport raw milk in specialised trucks to the production facilities. Due to their specialised nature, these trucks carried no load on the return leg.With production facilities closer to the milk source, pre-packed products can now be transported on conventional trucks, with a second payload on the return leg, significantly reducing Clover’s transportation costs.
- Sustainable supply
- Sustainable milk supply
Clover is one of few large dairy processors who have a longstanding history of purchasing milk from previously disadvantaged producers. Economic factors and sustainable milk quality are the largest barriers to entry for these farmers. Likewise, a number of Black Economic Empowerment (“BEE”) initiatives have failed due to a lack in expertise, support and dedication at farm level. There are, however a number of very good examples of commercial producers partnering with communities and labour. Most of these projects were initiated by Amadlelo Agri (www.amadlelo.co.za) and are sustainable.
Sustainable supply is ensured through Clover’s Unique Milk Procurement System (CUMPS) and the Company pays a market related price for raw milk. The Best Farming Practice (“BFP”) programme further assists producers to increase efficiency and become more sustainable.
The downward trend in the Group’s milk producer numbers is a result of continuous consolidation in the primary industry and is not a threat to the sustainability of milk supply in the short- to medium term, but does have an impact on job creation, as bigger producers tend to mechanise more. The consolidation of milk producers and high barriers to entry, especially for emerging farmers is not in the best interest of rural development or job creation. It is therefore very important for the industry and government to find a way of ensuring a viable agricultural sector and dairy industry.
- Sustainable milk supply
Sustainable milk supply
Description | 2013 | 2012 | 2011 | 2010 | 2009 |
Litres of milk procured (Million litres) | 667,7 | 648,2 | 652,4 | 608,2 | 638,7 |
---|---|---|---|---|---|
Litres of raw milk transported per kilometre | 70,3 | 69,0 | 73,4 | 80,0 | 88,0 |
Number of milk producers who supplied milk to Clover during the year |
240 | 258 | 293 | 309 | 353 |
Estimated number of employees employed by above producers* | 3 637 | 3 738 | 4 102 | 4 326 | 4924 |
Estimated number of dependants reliant on income received from above employees** | 13 656 | 18 690 | 20 510 | 21 630 | 24710 |
Future
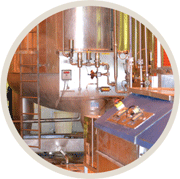
Cielo Blu focus
Pinetown production
- Installed a steriliser (18 000 litres/hr).
- Installed aseptic tank storage.
- Installed a UHT filling line (1000 Slimline) bringing the total to 4.
- Upgraded utilities.
- Plant capacity increased by 30m litres per year.
- Created 14 additional jobs.
Clover is cognisant of the fact that integrated reporting is a phased approach. The Group continues to collect, collate and report on an increasing number of key sustainability performance data to enhance the overall quality of Clover’s performance in this regard.
The Group remains committed to continuous improvement in all matters that affect the sustainability of Clover and its activities.
Reporting
This Report of the Social and Ethics Committee will be presented by one of its members to the Company’s Annual General Meeting. In the opinion of the members of the Committee this report fairly presents the standing of the Company and Group in relation to the matters specified in regulation 43 to the Companies Act 2008 for the year ended 30 June 2013.
TA Wixley
Chairman