Ethical operations – reporting on the 6 capitals
Manufactured Capital
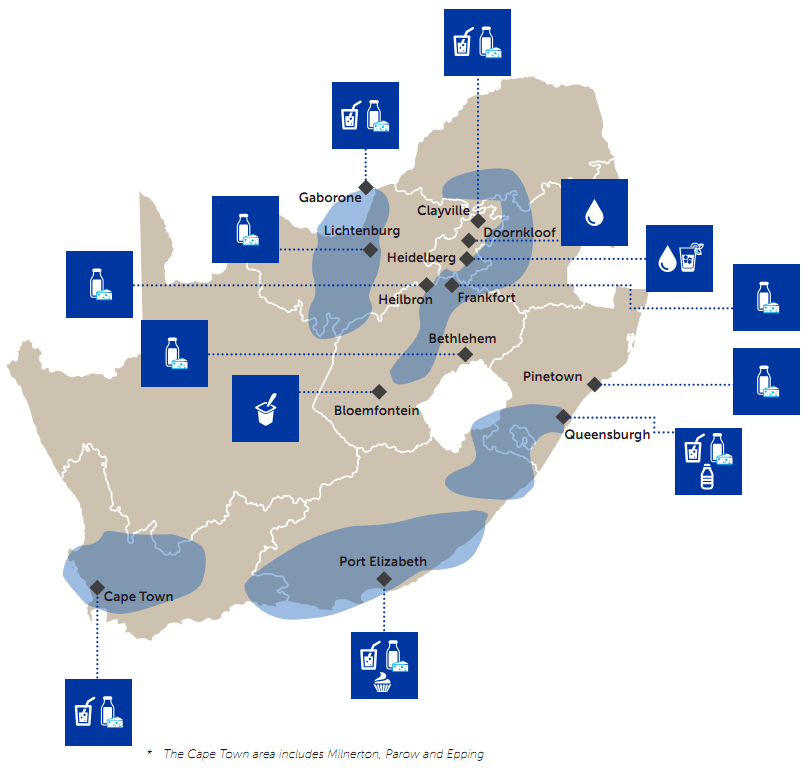
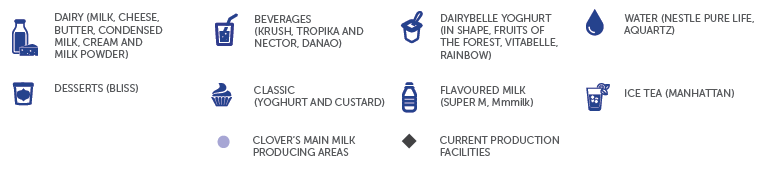
This table depicts salient features of Clover's manufactured capital: | ||
Producer selection | As at 30 June 2016, Clover sources its milk from 155 carefully selected collection points. | |
Ongoing quality assurance | 55 quality checks are performed on fresh milk from when it is collected at the farm to when it reaches the shelf. | |
Clover Way Better approach to work | Clover's production systems are flushed every 8 hours to ensure freshness. | |
Clover Way Better supply chain and warehousing capabilities |
Delivering to approximately 20 545 points through 548 trucks to an average of 8 customers per day per truck. |
Supply chain planning and procurement
Clover's Supply Chain Planning department centrally plans all manufacturing, purchasing, storing and deployment of finished goods throughout Clover's integrated supply chain. Production requirements, stock levels and deployment plans are based on predicted future market demand for Clover's products. Consumer demand is predicted through a sales and operations planning process that utilises statistical forecasting models. These results are further checked in collaboration with Clover Commercial and Clover Marketing. The seasonal nature of raw milk supply requires careful production planning that takes into account raw milk intake, desired stock levels and capacity constraints in Clover's production and distribution network. Milk flow from procurement depots to factories is optimised daily to ensure the lowest possible landed cost of milk at factory gate. Clover's Executive Committee directs the Supply Chain Planning department to act well in time to prevent potential demand versus supply imbalances.
The Supply Chain Planning department is also responsible for managing all primary transportation between factories and distribution depots, as well as bulk deliveries to selected customers. Primary transportation is executed through a combination of Clover managed vehicles and external hauliers. Our primary objective is to optimise the mix between own managed fleet and external hauliers, while ensuring the sustainability of these activities at a competitive cost.
Clover is continuously improving processes to ensure customer demand is met at the most competitive cost. The following initiatives to create long term value are currently in progress:
Integrated Business Planning project
- State-of-the-art planning software is at present being introduced to replace the current legacy planning tools
- All systems are being aligned and integrated with Clover's Enterprise Resource Planning (ERP) system
- This system will enable faster and more efficient what-if modelling and optimisation strategies, supported by enhanced sales and operations (S&OP) planning
- Improved alignment between Operations, Commercial and Marketing will be achieved through enhanced communication and visibility planning.
Network optimisation
- Clover implemented a network optimisation model (Profit Point) that provides a simulation capability and optimisation engine to evaluate potential changes in the supply chain
- This tool is used regularly to initiate and/or evaluate potential future placements of production and distribution facilities in the network to ensure optimal use of supply chain infrastructure.
Clover's centralised procurement department is responsible for procuring ingredients and packaging materials from qualifying suppliers to provide consistently high quality materials for production. Clover's procurement philosophy is to build partnerships that shift the understanding beyond monetary considerations to also include socio-economic objectives and long-term value creation.
Milk procurement
As a market driven company, Clover sources its raw milk in volumes to match projected demand. Clover's unique milk procurement system (CUMPS) is instrumental to helping ensure that Clover sources and retains raw milk according to its needs. Raw milk quality is the key to the safety and wholesomeness of Clover's products. Clover regularly audits each and every farm where raw milk is produced and orders all its milk from farms with above 80% audit scores against Clover's Best Farming Practices.
Sustainable milk supply
Clover has been purchasing raw milk from farmers and producers for the last 118 years. We understand the importance of milk producers in the supply chain and hold them in high esteem for providing excellent quality raw milk, often under challenging circumstances. Globally and in South Africa the number of milk producers is diminishing. Although this decline is not necessarily a threat to sustainable milk supply, it does harm job creation, rural development and the financial wellbeing of rural communities. We therefore believe it is imperative that the industry and government find a way of ensuring a viable agricultural sector and dairy industry. Agriculture is the cornerstone of healthy rural development and food security.
Clover is currently working with government and Deloitte on an agricultural revival programme that utilises high potential unused land to empower emergent dairy farmers and connect them to shared milking schemes. In our view, emergent developing dairy farmers should be linked to commercial dairy farmers with the expertise to help develop fallow land into sustainable dairy farms. These linkages will enable the transfer of knowledge to emergent dairy farmers, bolstered by ongoing support and mentorship.
Key statistics for Clover milk procurement
Description | 2016 | 2015 | 2014 | 2013 | 2012 |
Milk intake from producers (Million litre) | 611 | 606 | 632 | 668 | 648 |
---|---|---|---|---|---|
Litres of milk transported per kilometre | 117 | 111 | 99 | 70 | 69 |
Average number of collection points | 169 | 189 | 218 | 240 | 258 |
Number of employees employed by milk producers* | 2 765 | 3 103 | 3 277 | 3 637 | 3 738 |
Number of dependants reliant on above employees** | 9 700 | 12 099 | 13 867 | 13 656 | 18 690 |
* | The number of employees is based on previous production cost survey statistics and feedback from producers. |
** | The number of dependants is based on feedback from producers. |
Raw milk quality and certification
Clover's commitment to quality commences on the farms selected to supply our raw milk. Clover utilises a Best Farming Practices (BFP) programme, based on International Dairy Federation guidelines, which emphasises:
- animal health and herd management
- animal feed and water
- animal medication and agricultural chemicals
- milk hygiene and safety
- environmental management
- personnel and people.
As a market driven company, Clover pays careful attention to the needs of our consumers. It is clear that consumers want natural milk products that are untainted by artificial hormones and inhibitors. Our producers have been instructed not to supply Clover with milk originating from cows treated with recombinant bovine somatotropin (rBST). Each and every milk producer for Clover has signed such a declaration. Every tanker load of milk is tested for inhibitors such as antibiotics. Milk that tests as positive for inhibitors is marked with a food colourant and discarded under controlled circumstances. Clover will leave no stone unturned to ensure that our products remain safe and nutritious.
Clover has evaluated various sustainable dairy farming models in recent years and concluded that developing our own integrated dairy farming system is not core to our operations or financially viable. We therefore selected the Global Gap programme and will soon appoint an accredited and independent certifying body to conduct audits on our behalf. Certification will be completely independent, as Clover personnel will no longer perform the audits. Our Producer Services personnel will, however, continue assisting our milk producers to become compliant and to retain their certification. The implementation of the Global Gap programme at farm level commenced on 1 July 2016.
Production
Once the raw milk has passed all quality tests, it is processed at Clover's 15 production facilities across South Africa and in certain African countries. Our products include fresh milk, UHT milk, flavoured milk, yoghurt, cheese, butter and milk powder, desserts, fruit juices, dairy fruit mix, water and iced tea. The base ingredient for our beverages is generally produced as a concentrate and is procured from carefully selected suppliers who guarantee consistently high quality products. The concentrate is mixed with good quality water to manufacture final products such as Krush Juice and Tropika. Natural groundwater sources are regularly tested for safety and quality. During the period under review, Clover acquired the UHT plant of Good Hope Beverages, which is situated in Milnerton, Cape Town.
Infrastructure
Clover owns the bulk of the properties from where we operate. Clover's buildings and equipment are comprehensively insured, including for potential loss of profit due to business interruptions. New and innovative technologies are enabling Clover to consolidate some of our facilities for cost efficiencies. Clover continuously seeks ways and means to reduce costs along the supply chain to ensure that we remain cost competitive, while also lessening our environmental impact. We have embedded the continuous improvement concept into the Clover culture, so that big and small improvements are properly identified, controlled and managed.
Given the speed of technological progress, businesses need to continually invest in improved efficiencies and cost reduction. Failure to do so could lead to an ineffective cost structure and an outdated and uncompetitive product offering. Clover therefore monitors the following key risk indicators:
- Depreciation vs capital expenditure
The quality of Clover's manufactured capital will deteriorate if we do not continually invest in it. Clover invests to improve efficiency and effectiveness rather than merely maintaining assets. Over the past three years we allocated substantial capital resource into enhancing the quality of our manufacturing assets. The graph below represents the capital investment for Clover's production facilities.
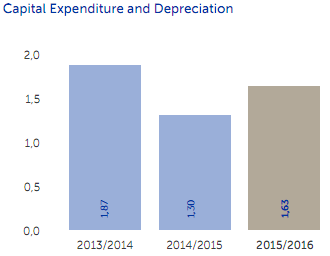
- Factory machine availability
Maintaining a high level of machine availability is vital for achieving higher throughput per hour, reducing product losses and reducing energy consumption. A further benefit is that assets are properly utilised, and the need for additional equipment to accommodate a higher level of production is reduced when availability improves. Clover's machine availability averages have increased substantially over the past five years.
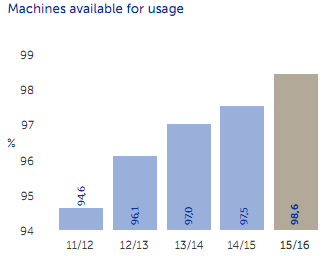
Best practice utilisation of production capacity
- Capacity utilisation
Sales growth is only possible if the manufacturing capacity exists to meet the higher volumes of production required. Clover's ability to manage manufacturing capacities is vital for ramping up to meet unexpected demand, or to reduce production when needed to keep unit production costs down. Clover's capacity utilisation per product group must remain within best practise parameters. Milk intake is seasonal, with an increased milk intake between August and January in any given year, so that certain factories work at full capacity in the seasonal peak cycle. Production reduces substantially in the off season. Clover's capacity during the seasonal peak determines limits for increased milk intake. As some products are highly seasonal, the average value and the peak (November) value have been utilised as being the most illustrative.
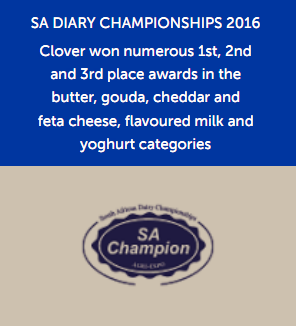
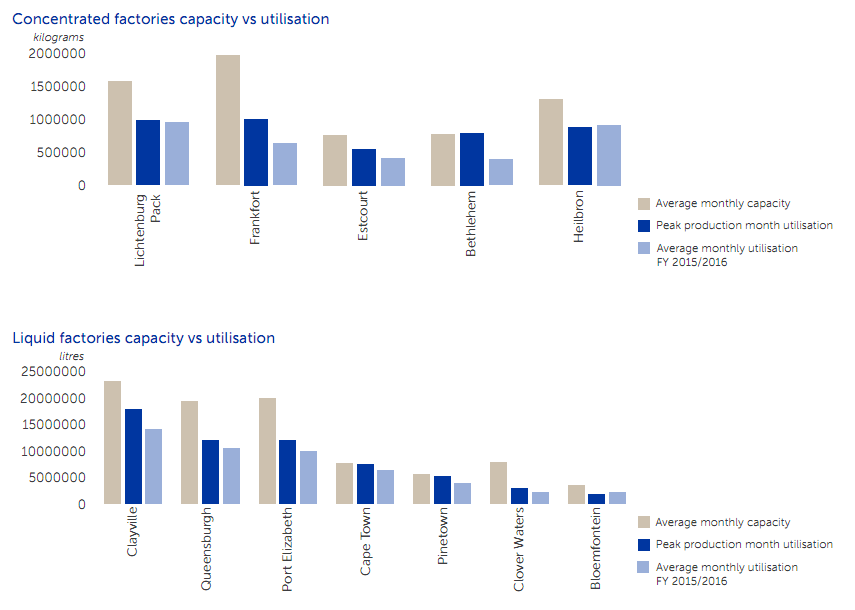
- Material trade-offs and interdependencies between capitals
Continuous improvement and advancing technology directly impacts Clover's natural and human capitals. This requires continuous improvement in skill levels over time. The introduction of new working methods impacts on the amount of labour required per unit of production. As a result, Clover needs to measure production per man hour to help evaluate how Clover succeeds in improving output per labour hour worked, thereby reducing the total operational cost of the business. Productivity increased substantially in the 2015/16 financial year. Clover is investing in automation for repetitive tasks, improved software and working methods to keep on raising productivity.
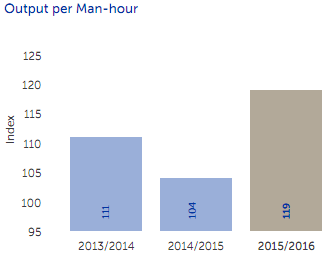
Occupational Health and Safety
Clover has a responsibility to provide safe and healthy working environments. Formal health and safety policies are in place, and are monitored. Standard health and safety procedures exist for every potentially dangerous substance or operation in the workplace. All of Clover's production facilities and distribution facilities were audited during the review period, for compliance with all applicable environmental legislation and the Occupational Health and Safety Act (OHS). Annual audits evaluate continuous health and safety improvement, supported by independent verification audits conducted every three years. Clover's Lost Time Injury Frequency (LTIF) rate, based on reportable injuries per million man-hours worked, improved on the previous year. The following table aggregates current Clover health and safety statistics. The number of people trained in health and safety reduced in the current year as this is not an annual requirement.
Supply chain | ||
Description | 2015 | 2016 |
Number of people receiving Health and Safety training (1 Person, 1 Course = 1) | 1 090 | 421 |
---|---|---|
Fatalities – People working under our control | 1 | 1 |
Total Number of Recordable Injuries, including Medically Treated Cases, Lost Time Injuries and Fatalities | 434 | 610 |
First Aid Cases – Persons working under our control | 626 | 566 |
Reportable (Compensation Commissioner) lost time injuries for this financial year | 147 | 43 |
Fatal Injury Frequency Rate (i.e. number of Fatalities per 200 000 person hours worked)1 | 0,0011 | 0,011 |
Lost Time Injury Frequency Rate (i.e. the number of LTIs per 200 000 person hours worked) | 0,638 | 0,562 |
1 Please note figure for previous year has been restated.
The following table lists Clover's Occupational Health and Safety appointees responsible for ensuring that all Clover premises comply with the highest safety requirements:
Executive summary | 2015 | 2016 |
16.2 and Assistant1 | 37 | 27 |
---|---|---|
Section 8.22 | 39 | 87 |
GMR23 | 28 | 11 |
SHE Reps4 | 234 | 238 |
Firefighters | 277 | 211 |
First aiders | 296 | 255 |
Stacking supervisors | 24 | 47 |
Accident investigators | 99 | 114 |
Emergency coordinators | 30 | 40 |
Occupational Health Nurses5 | 19 | 12 |
SHE Officer/Manager | – | 15 |
1 | In terms of the Occupational, Health and Safety Act, a 16.2 appointment is a person appointed by the CEO of a company, who is responsible for all Health and Safety matters of the company and will be subject to the control and direction of the CEO. |
2 | In terms of the Occupational Health and Safety Act, an 8.2 appointment is a person appointed to facilitate the occupational safety of the company. |
3 | This appointment is in terms of the General Machinery Regulations. The designated person is appointed in a full-time capacity in respect of each premise on which machinery is used to supervise all machinery. |
4 | Safety, health and environmental representative who represent all employees of the business. |
5 | In 2015, Occupational Health Nurses and SHE Officers were reported in a combined figure of 19. |
Distribution
Clover's Primary Distribution Department moves all our products from factories to distribution facilities across South Africa. Every day, our Customer Call Centre receives electronic or telephonic customer orders and arranges deliveries from one of Clover's 25 distribution centres to approximately 20 545 delivery points in South Africa. Clover also has agreements with several major customers, for whom we provide distribution and in-store merchandising services.
Stores receive direct deliveries of Clover products between two and five times per week, depending on sales volumes. Clover has over 548 delivery vehicles that deliver stock to approximately 20 545 delivery points. Over 800 SKU (stock keeping units) are stored, picked, delivered and merchandised in Clover's distribution network. More than 50% of all refrigerated dairy and processed meat products of all brands delivered to stores in South Africa are transported through the Clover Distribution Network.
Besides specialising in the distribution and sales of chilled products, Clover also handles significant quantities of non-perishable food products. Customers serviced by Clover include:
The wide ranging distribution of products on behalf of third parties provides one of Clover's most valuable revenue streams.
Below is a depiction of Clover's distribution centres in South Africa:
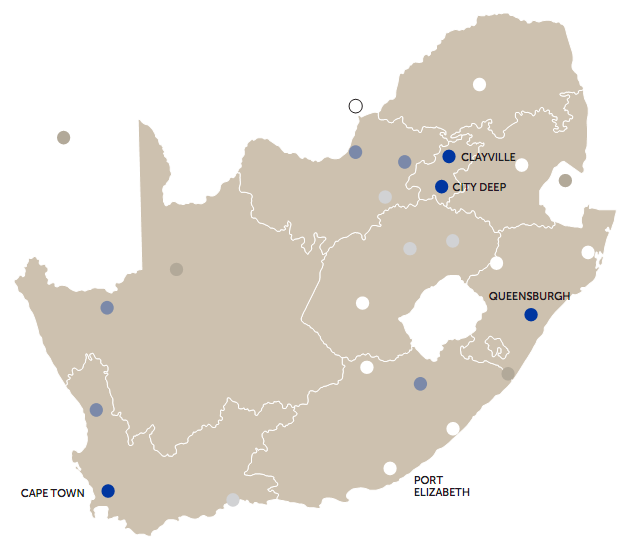
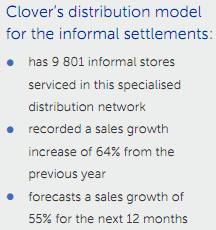
Masakhane – “let's build together”
Masakhane (literally meaning “Let's build together”) got off the ground in 2012 as Clover's first targeted approach to informal trading environments. The Masakhane objective is to grow sales in stores that do not form part of a Clover Key Account or Buying Group. Masakhane has enabled Clover to rapidly increase our reach into informal trading scenarios such as shacks, spaza shops, tuck shops, corner cafés, general traders and bottle stores.
Masakhane's initial 2012 customer base of 600 stores, has since expanded rapidly to 9801 informal stores. Sales growth for the Masakhane project over the last year was 64%, albeit off a small base. The Masakhane channel is poised for a forecasted 55% growth in sales over the next financial year.
Clover's emerging market sales channel
Recent Nielsen research shows that spending at South Africa's informal stores account for 20% of all cash spent annually. These stores sold goods to the value of R64 billion last year and are growing their sales at 7% per annum, while formal stores are only registering 4% sales growth. This emerging market is not a single entity, but is a multitude of small informal stores, spazas, superettes and traders.
Clover's Masakhane emerging market sales channel is aimed directly at the informal store owners and customers, based on the backbone of Clover's national distribution network. By offering Clover and other branded products directly to these stores, Masakhane is a game changer in the industry. Informal stores now have access to quality products at affordable prices, which attracts new customers to the informal stores and creates a demand for nutritional products.
Clover Masakhane provides training directly to the informal store owners to provide the required commercial and supply chain expertise to further develop and sustain their stores. Masakhane is a definite catalyst for growth and job creation in the emerging market.
Clover Masakhane aims to create 1004 new and permanent jobs within the distribution and retail sector by 2020. Clover Masakhane recruits undergo sales and distribution training that equip Clover Masakhane entrepreneurs with the ability to carry out their daily responsibilities while preparing and developing them for formal trade.
Quality
Quality control over final product
All Clover products are produced in terms of international best practices for quality, hygiene and food safety. These are only formally released by the Quality department once assessed against these specifications. All South African Clover factories are HACCP certified and accredited by third party auditors. We comply with all international standards required for food safety and quality risk management systems. Clover Quality Assurance and Control deploys highly trained technicians in well-equipped laboratories to test our products at all production stages.
In this year of review, Clover implemented a programme to upgrade all our quality systems to comply with the latest and world-wide accepted FSSC 22000 Quality Management system. FSSC 22000 principles are being implemented throughout the value chain. Clover also introduced a Supplier Quality Control programme to ensure that all raw materials and packaging materials comply with internationally recognised food safety requirements.
Value creation
Clover's recent investments in upgrading our manufactured capital is building long term value for our stakeholders. We foresee future value creation in manufactured capital as follows:
Supply chain planning and procurement
- Improve pricing strategy with suppliers and other role-players
- Integrate supply chain modelling
- Integrate business planning
- Procurement – supplier collaboration
- Development of suppliers to limit the risk of milk shortages
- Improve Clover's B-BBEE status and promote job creation
- Milk procurement – supplier collaboration to commence export initiatives and promote growth in national dairy industry.
Production
- Improve asset utilisation through consolidation
- Promote industry development, export opportunities and job creation
- Carbon footprint reduction
- Dairy industrial park for all concentrated products
- Increase capacity utilisation.
Distribution
- Optimise the distribution network through real time monitoring of execution
- Distribution mobility by delivering a paperless system to promote streamlined product returns and driver reconciliations
- Distribution retailer centralisation
- Expand basket of principal products through strategic partnership focus
- Collaboration with customers.
Commercial
- Acquire new customers
- Retain and grow current customers
- Identify and enter untouched markets
- Acquire and invest in higher margin products
- Focus on all segments of the market, both formal and informal.